Budowa maszyn roboczych to złożony proces, który obejmuje wiele różnych elementów i komponentów. Każda maszyna robocza składa się z kilku kluczowych części, które współpracują ze sobą w celu wykonania określonych zadań. Podstawowe elementy budowy maszyn roboczych to między innymi silnik, układ napędowy, ramy oraz systemy sterowania. Silnik jest sercem maszyny, odpowiedzialnym za generowanie mocy potrzebnej do jej działania. Układ napędowy przekształca moc silnika na ruch mechaniczny, co pozwala na wykonywanie pracy. Rama stanowi szkielet maszyny, zapewniając jej stabilność i wytrzymałość. Systemy sterowania umożliwiają operatorowi kontrolowanie działania maszyny, co jest kluczowe dla bezpieczeństwa i efektywności pracy. W zależności od przeznaczenia maszyny, mogą być również stosowane dodatkowe elementy, takie jak hydraulika czy elektronika, które zwiększają jej funkcjonalność i możliwości operacyjne.
Jakie są najczęstsze zastosowania maszyn roboczych w przemyśle
Maszyny robocze znajdują szerokie zastosowanie w różnych branżach przemysłowych, co czyni je niezbędnym narzędziem w nowoczesnej produkcji. W przemyśle budowlanym maszyny takie jak koparki czy dźwigi są wykorzystywane do wykonywania ciężkich prac ziemnych oraz transportu materiałów budowlanych. W branży rolniczej natomiast spotykamy ciągniki oraz kombajny, które ułatwiają zbieranie plonów oraz uprawę ziemi. W przemyśle motoryzacyjnym maszyny robocze są wykorzystywane do montażu i produkcji pojazdów, a także do testowania ich wydajności i bezpieczeństwa. W sektorze energetycznym maszyny te odgrywają kluczową rolę w procesach wytwarzania energii, zarówno z odnawialnych źródeł, jak i tradycyjnych paliw. Dzięki zastosowaniu nowoczesnych technologii, takich jak automatyka czy robotyzacja, maszyny robocze stają się coraz bardziej zaawansowane i efektywne, co przekłada się na zwiększenie wydajności produkcji oraz redukcję kosztów operacyjnych.
Jakie są najnowsze technologie w budowie maszyn roboczych
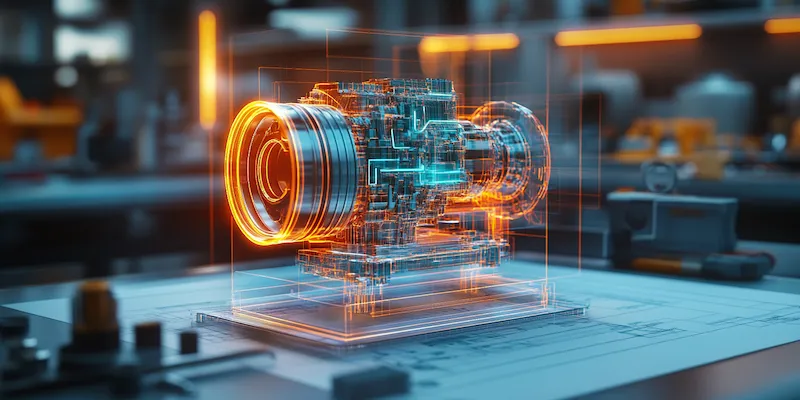
W ostatnich latach obserwujemy dynamiczny rozwój technologii związanych z budową maszyn roboczych, co znacząco wpływa na ich wydajność oraz funkcjonalność. Jednym z najważniejszych trendów jest automatyzacja procesów produkcyjnych, która pozwala na zwiększenie precyzji oraz redukcję błędów ludzkich. Roboty przemysłowe stają się coraz bardziej powszechne w fabrykach, gdzie wykonują powtarzalne zadania z dużą dokładnością. Kolejnym istotnym aspektem jest zastosowanie sztucznej inteligencji w systemach sterowania maszynami roboczymi. Dzięki algorytmom uczenia maszynowego możliwe jest optymalizowanie procesów produkcyjnych oraz przewidywanie awarii zanim one wystąpią. Technologie druku 3D również zaczynają odgrywać ważną rolę w budowie maszyn roboczych, umożliwiając szybkie prototypowanie oraz produkcję skomplikowanych komponentów bez potrzeby korzystania z tradycyjnych metod obróbczych. Dodatkowo rozwój technologii IoT (Internet of Things) pozwala na monitorowanie pracy maszyn w czasie rzeczywistym oraz zbieranie danych analitycznych, co przyczynia się do lepszego zarządzania zasobami i zwiększenia efektywności operacyjnej.
Jakie są kluczowe wyzwania w budowie nowoczesnych maszyn roboczych
Budowa nowoczesnych maszyn roboczych wiąże się z wieloma wyzwaniami technologicznymi oraz organizacyjnymi, które należy pokonać, aby osiągnąć sukces na rynku. Jednym z głównych wyzwań jest konieczność dostosowania się do szybko zmieniających się wymagań klientów oraz standardów branżowych. Klienci oczekują coraz bardziej zaawansowanych technologicznie rozwiązań, które jednocześnie będą łatwe w obsłudze i niezawodne. Kolejnym istotnym problemem jest integracja różnych systemów technologicznych w jedną spójną całość. W miarę jak maszyny stają się coraz bardziej skomplikowane i wyposażone w różnorodne technologie, inżynierowie muszą znaleźć sposób na ich efektywne połączenie i współpracę. Również kwestie związane z ekologią i zrównoważonym rozwojem stają się coraz ważniejsze – producenci muszą dążyć do ograniczenia negatywnego wpływu swoich produktów na środowisko naturalne poprzez stosowanie materiałów ekologicznych oraz energooszczędnych rozwiązań.
Jakie są kluczowe aspekty bezpieczeństwa w budowie maszyn roboczych
Bezpieczeństwo w budowie maszyn roboczych jest jednym z najważniejszych aspektów, który musi być brany pod uwagę na każdym etapie projektowania i produkcji. W miarę jak maszyny stają się coraz bardziej zaawansowane technologicznie, rośnie również ryzyko związane z ich użytkowaniem. Dlatego istotne jest, aby inżynierowie i projektanci przestrzegali norm oraz standardów bezpieczeństwa, które mają na celu minimalizowanie zagrożeń dla operatorów oraz osób znajdujących się w pobliżu. Kluczowym elementem bezpieczeństwa jest odpowiednie zaprojektowanie systemów sterowania, które powinny być intuicyjne i łatwe w obsłudze, a także wyposażone w funkcje awaryjnego zatrzymania. Dodatkowo ważne jest przeprowadzanie regularnych szkoleń dla operatorów maszyn, aby zapewnić im wiedzę na temat bezpiecznego użytkowania sprzętu oraz procedur postępowania w sytuacjach awaryjnych. Warto również inwestować w nowoczesne technologie monitorujące, które pozwalają na bieżąco śledzić stan maszyny oraz wykrywać potencjalne usterki zanim doprowadzą one do poważnych awarii.
Jakie są trendy w projektowaniu maszyn roboczych na przyszłość
Projektowanie maszyn roboczych ewoluuje w odpowiedzi na zmieniające się potrzeby rynku oraz rozwój technologii. W przyszłości możemy spodziewać się dalszego wzrostu znaczenia automatyzacji i robotyzacji procesów produkcyjnych. Maszyny będą coraz bardziej zintegrowane z systemami sztucznej inteligencji, co pozwoli na samodzielne podejmowanie decyzji oraz optymalizację działań w czasie rzeczywistym. Również rozwój technologii Internetu Rzeczy (IoT) umożliwi lepsze monitorowanie pracy maszyn oraz zbieranie danych analitycznych, co przyczyni się do zwiększenia efektywności operacyjnej. Kolejnym trendem będzie dążenie do zrównoważonego rozwoju – projektanci będą musieli uwzględniać aspekty ekologiczne już na etapie koncepcji maszyn, stosując materiały przyjazne dla środowiska oraz rozwiązania energooszczędne. Warto również zwrócić uwagę na ergonomię projektowanych maszyn, aby zapewnić komfort i bezpieczeństwo operatorom podczas pracy. Przyszłość budowy maszyn roboczych to także większa personalizacja produktów dostosowanych do indywidualnych potrzeb klientów, co pozwoli na lepsze wykorzystanie ich możliwości w różnych branżach przemysłowych.
Jakie są najważniejsze wyzwania związane z konserwacją maszyn roboczych
Konserwacja maszyn roboczych jest kluczowym elementem zapewniającym ich długotrwałe i efektywne działanie. Jednakże wiąże się to z wieloma wyzwaniami, które mogą wpływać na wydajność produkcji oraz koszty operacyjne. Jednym z głównych problemów jest konieczność regularnego przeprowadzania przeglądów technicznych oraz konserwacji, co wymaga odpowiednich zasobów ludzkich i finansowych. Wiele firm boryka się z brakiem wykwalifikowanego personelu zdolnego do przeprowadzania skomplikowanych napraw czy diagnostyki maszyn. Dodatkowo nieprzewidziane awarie mogą prowadzić do przestojów w produkcji, co generuje dodatkowe koszty i straty finansowe. Właściwe zarządzanie konserwacją wymaga również zastosowania nowoczesnych technologii monitorujących stan maszyn, co pozwala na przewidywanie potencjalnych usterek i planowanie działań serwisowych przed wystąpieniem awarii. Warto również zwrócić uwagę na znaczenie dokumentacji związanej z konserwacją – jej brak może prowadzić do nieefektywnego zarządzania procesami serwisowymi oraz utrudniać identyfikację problemów.
Jakie są korzyści wynikające z modernizacji istniejących maszyn roboczych
Modernizacja istniejących maszyn roboczych to proces, który może przynieść wiele korzyści zarówno dla przedsiębiorstw, jak i dla ich pracowników. Przede wszystkim modernizacja pozwala na zwiększenie wydajności produkcji poprzez wdrożenie nowoczesnych technologii oraz usprawnienie procesów operacyjnych. Dzięki temu firmy mogą osiągnąć lepsze wyniki finansowe oraz zwiększyć swoją konkurencyjność na rynku. Kolejną zaletą modernizacji jest poprawa jakości produktów – nowoczesne maszyny często oferują wyższą precyzję i dokładność wykonania, co przekłada się na lepszą jakość finalnych wyrobów. Dodatkowo modernizacja może przyczynić się do obniżenia kosztów eksploatacji poprzez zastosowanie energooszczędnych rozwiązań oraz materiałów o lepszej trwałości. Ważnym aspektem jest również poprawa warunków pracy dla operatorów – nowoczesne maszyny często są bardziej ergonomiczne i łatwiejsze w obsłudze, co wpływa na komfort pracy i zmniejsza ryzyko urazów zawodowych.
Jakie są różnice między maszynami roboczymi a urządzeniami przemysłowymi
Maszyny robocze i urządzenia przemysłowe to terminy często używane zamiennie, jednak istnieją między nimi istotne różnice dotyczące ich funkcji oraz zastosowania. Maszyny robocze zazwyczaj odnoszą się do sprzętu wykorzystywanego do wykonywania konkretnych zadań mechanicznych lub fizycznych, takich jak koparki czy prasy hydrauliczne. Ich głównym celem jest wykonywanie pracy związanej z obróbką materiałów lub transportem ciężkich ładunków. Z kolei urządzenia przemysłowe obejmują szerszą gamę sprzętu wykorzystywanego w procesach produkcyjnych, takich jak linie montażowe czy systemy transportowe. Urządzenia te mogą być zarówno mechaniczne, jak i elektroniczne i często pełnią rolę wspomagającą dla maszyn roboczych. Ponadto urządzenia przemysłowe mogą być bardziej złożone pod względem integracji z systemami zarządzania produkcją oraz automatyki przemysłowej.
Jakie są kluczowe czynniki wpływające na wybór odpowiednich maszyn roboczych
Wybór odpowiednich maszyn roboczych to kluczowy krok dla każdej firmy zajmującej się produkcją lub świadczeniem usług wymagających użycia sprzętu mechanicznego. Istnieje wiele czynników wpływających na ten wybór, które należy dokładnie rozważyć przed podjęciem decyzji. Przede wszystkim istotna jest analiza specyfiki wykonywanej pracy – różne branże wymagają różnych rozwiązań technologicznych dostosowanych do ich potrzeb. Ważnym czynnikiem jest również wydajność maszyny – im wyższa wydajność, tym większa efektywność produkcji oraz mniejsze koszty operacyjne. Kolejnym aspektem jest koszt zakupu oraz eksploatacji maszyny – przedsiębiorcy muszą brać pod uwagę nie tylko cenę zakupu sprzętu, ale także koszty serwisowania czy zużycia energii. Niezwykle istotna jest także dostępność części zamiennych oraz wsparcia technicznego ze strony producenta – brak tych elementów może prowadzić do długotrwałych przestojów w produkcji w przypadku awarii maszyny.