Destylarka do rozpuszczalnika to urządzenie, które wykorzystuje proces destylacji do oddzielania różnych substancji na podstawie ich temperatury wrzenia. W praktyce oznacza to, że rozpuszczalnik, który chcemy odzyskać lub oczyścić, jest podgrzewany do momentu, w którym zaczyna parować. Para ta następnie przechodzi przez system chłodzenia, gdzie skrapla się i zbiera w osobnym naczyniu. Proces ten jest niezwykle efektywny i pozwala na uzyskanie wysokiej czystości rozpuszczalników, co jest kluczowe w wielu branżach, takich jak chemia czy farmacja. Warto zauważyć, że różne rodzaje rozpuszczalników mają różne temperatury wrzenia, co umożliwia ich selektywne oddzielanie. Na przykład, w przypadku destylacji mieszaniny etanolu i wody, etanol odparowuje w niższej temperaturze, co pozwala na jego łatwe oddzielenie. Destylarki mogą być zarówno proste, jak i bardziej zaawansowane technologicznie, z dodatkowymi funkcjami takimi jak automatyczne sterowanie temperaturą czy monitorowanie jakości destylatu.
Jakie są zalety używania destylarki do rozpuszczalnika
Używanie destylarki do rozpuszczalnika niesie ze sobą szereg korzyści, które są istotne zarówno dla przemysłu, jak i dla użytkowników indywidualnych. Przede wszystkim, główną zaletą jest możliwość odzyskiwania cennych substancji chemicznych, co przyczynia się do oszczędności materiałowych oraz redukcji odpadów. W kontekście ochrony środowiska, destylacja pozwala na zmniejszenie ilości niebezpiecznych odpadów chemicznych poprzez ich ponowne wykorzystanie. Kolejnym atutem jest wysoka jakość uzyskiwanych produktów; dzięki precyzyjnemu procesowi destylacji można osiągnąć bardzo wysoką czystość rozpuszczalników. Dodatkowo, nowoczesne destylarki są często wyposażone w systemy monitorujące i automatyzujące procesy, co zwiększa bezpieczeństwo pracy oraz wygodę użytkowania. Możliwość dostosowania parametrów pracy urządzenia do specyficznych potrzeb użytkownika sprawia, że destylarki stają się coraz bardziej popularnym rozwiązaniem w laboratoriach oraz warsztatach rzemieślniczych.
Jakie są najczęstsze zastosowania destylarki do rozpuszczalnika
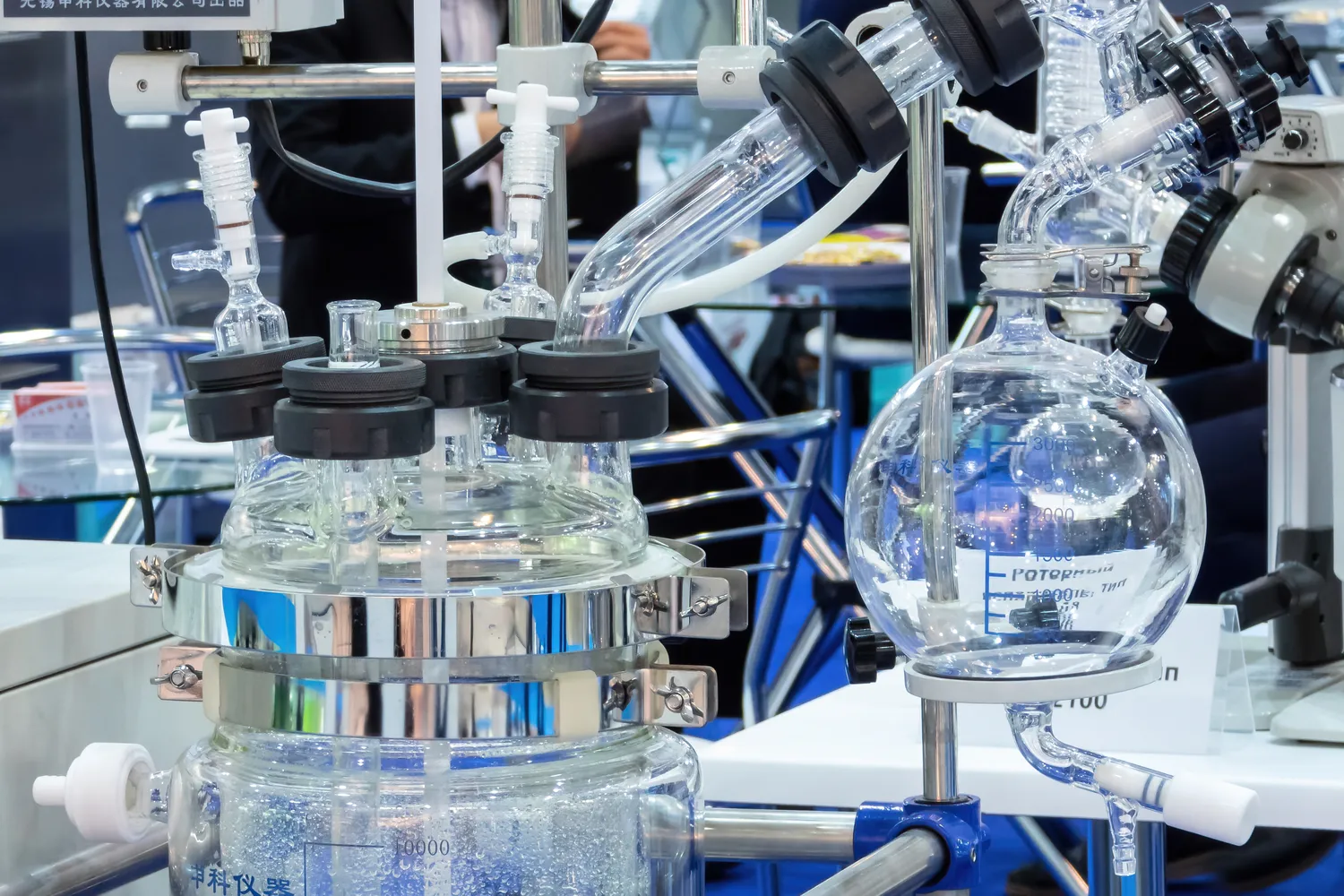
Destylarka do rozpuszczalnika znajduje szerokie zastosowanie w różnych dziedzinach przemysłu oraz nauki. Jednym z najczęstszych zastosowań jest odzyskiwanie rozpuszczalników organicznych używanych w procesach produkcyjnych oraz laboratoryjnych. Dzięki temu możliwe jest nie tylko oszczędzanie kosztów związanych z zakupem nowych surowców, ale także minimalizacja wpływu na środowisko poprzez ograniczenie ilości odpadów chemicznych. W laboratoriach chemicznych destylarki są wykorzystywane do oczyszczania reagentów oraz produktów reakcji chemicznych, co pozwala na uzyskanie wysoce czystych substancji niezbędnych do dalszych badań. W przemyśle farmaceutycznym destylacja odgrywa kluczową rolę w produkcji leków oraz substancji czynnych; dzięki niej można skutecznie oddzielać składniki aktywne od zanieczyszczeń. Ponadto, destylarki znajdują zastosowanie w przemyśle kosmetycznym przy produkcji perfum oraz innych kosmetyków zawierających lotne składniki zapachowe.
Jak wybrać odpowiednią destylarkę do rozpuszczalnika
Wybór odpowiedniej destylarki do rozpuszczalnika może być kluczowy dla efektywności procesu destylacji oraz jakości uzyskiwanych produktów. Na początku warto zastanowić się nad rodzajem substancji, które będą poddawane destylacji; różne modele mogą mieć różne zakresy temperatury oraz wydajności. Ważnym aspektem jest również pojemność urządzenia; dla użytku domowego wystarczające będą mniejsze modele, natomiast w przemyśle warto zainwestować w większe i bardziej wydajne urządzenia. Kolejnym czynnikiem jest materiał wykonania; stal nierdzewna zapewnia trwałość i odporność na korozję, co jest istotne przy pracy z agresywnymi chemikaliami. Dodatkowo warto zwrócić uwagę na funkcje dodatkowe takie jak automatyczne sterowanie temperaturą czy systemy chłodzenia; te udogodnienia mogą znacząco zwiększyć komfort użytkowania oraz bezpieczeństwo pracy.
Jakie są najczęstsze problemy z destylarką do rozpuszczalnika
Podczas korzystania z destylarki do rozpuszczalnika mogą wystąpić różne problemy, które mogą wpłynąć na efektywność procesu oraz jakość uzyskiwanych produktów. Jednym z najczęstszych problemów jest niewłaściwe ustawienie temperatury, co może prowadzić do niepełnej destylacji lub przegrzania substancji. Przegrzewanie może skutkować niepożądanymi reakcjami chemicznymi, które zmieniają skład destylatu. Kolejnym problemem jest zatykanie się rur chłodzących, co może być spowodowane osadami lub zanieczyszczeniami w używanych substancjach. Zatykanie to prowadzi do obniżenia efektywności chłodzenia i może skutkować wyciekiem pary. Warto również zwrócić uwagę na jakość używanych materiałów; niskiej jakości uszczelki czy elementy wykonane z nieodpowiednich tworzyw mogą prowadzić do wycieków lub reakcji chemicznych, które są niebezpieczne dla użytkownika. Dodatkowo, niewłaściwe użytkowanie urządzenia, takie jak brak regularnego czyszczenia czy konserwacji, może prowadzić do szybszego zużycia elementów oraz obniżenia wydajności.
Jakie materiały są najlepsze do budowy destylarki do rozpuszczalnika
Wybór odpowiednich materiałów do budowy destylarki do rozpuszczalnika ma kluczowe znaczenie dla jej wydajności oraz bezpieczeństwa użytkowania. Najczęściej stosowanym materiałem jest stal nierdzewna, która charakteryzuje się wysoką odpornością na korozję oraz działanie agresywnych substancji chemicznych. Stal nierdzewna zapewnia również trwałość i długowieczność urządzenia, co jest istotne w kontekście intensywnego użytkowania w laboratoriach czy przemyśle. Innym popularnym materiałem jest szkło borokrzemowe, które jest odporne na wysokie temperatury oraz chemikalia. Szkło pozwala na łatwe monitorowanie procesu destylacji, ponieważ użytkownik ma możliwość obserwacji zachodzących reakcji. W przypadku elementów takich jak uszczelki czy węże warto wybierać materiały silikonowe lub teflonowe, które są odporne na działanie większości chemikaliów i wysokich temperatur. Dobrze dobrane materiały nie tylko zwiększają bezpieczeństwo pracy, ale także wpływają na jakość uzyskiwanych produktów; niektóre materiały mogą reagować z substancjami chemicznymi, co prowadzi do zanieczyszczeń w destylacie.
Jakie są różnice między destylarkami a innymi metodami oczyszczania
Destylarka do rozpuszczalnika różni się od innych metod oczyszczania substancji chemicznych pod względem zasady działania oraz efektywności. Podczas gdy destylacja polega na wykorzystaniu różnicy temperatur wrzenia, inne metody oczyszczania mogą opierać się na filtracji, adsorpcji czy ekstrakcji cieczy. Na przykład filtracja polega na oddzieleniu cząstek stałych od cieczy za pomocą filtrów, co jest skuteczne w przypadku zawiesin, ale niekoniecznie sprawdzi się przy separacji rozpuszczalników o podobnych temperaturach wrzenia. Z kolei metoda adsorpcji wykorzystuje zdolność niektórych materiałów do wiązania cząsteczek z cieczy; chociaż jest to skuteczna metoda oczyszczania, może być mniej efektywna w przypadku dużych ilości rozpuszczalników. Ekstrakcja cieczy polega na wykorzystaniu innego rozpuszczalnika do oddzielenia pożądanych składników; ta metoda również ma swoje ograniczenia związane z kompatybilnością chemiczną używanych substancji.
Jakie przepisy regulują używanie destylarki do rozpuszczalnika
Używanie destylarki do rozpuszczalnika podlega różnym przepisom prawnym i regulacjom, które mają na celu zapewnienie bezpieczeństwa użytkowników oraz ochrony środowiska. W wielu krajach istnieją szczegółowe przepisy dotyczące obrotu substancjami chemicznymi oraz ich przetwarzania; często wymagają one posiadania odpowiednich zezwoleń oraz certyfikatów dla osób zajmujących się destylacją. W Polsce przepisy te regulowane są przez Ustawę o substancjach chemicznych oraz Ustawę o ochronie środowiska, które nakładają obowiązki zarówno na producentów, jak i użytkowników urządzeń destylacyjnych. Osoby korzystające z destylarek powinny również przestrzegać zasad BHP oraz norm dotyczących przechowywania i transportu substancji chemicznych. Dodatkowo, w przypadku stosowania destylarek w laboratoriach czy zakładach przemysłowych konieczne może być wdrożenie systemu zarządzania jakością zgodnego z normami ISO lub innymi standardami branżowymi.
Jakie są koszty zakupu i eksploatacji destylarki do rozpuszczalnika
Koszty zakupu i eksploatacji destylarki do rozpuszczalnika mogą znacznie się różnić w zależności od modelu urządzenia oraz jego przeznaczenia. Na rynku dostępne są zarówno proste modele przeznaczone dla hobbystów, jak i zaawansowane systemy przemysłowe o dużej wydajności. Ceny podstawowych destylarek zaczynają się od kilkuset złotych, natomiast profesjonalne urządzenia mogą kosztować kilka tysięcy złotych lub więcej. Oprócz kosztu zakupu należy uwzględnić również wydatki związane z eksploatacją urządzenia; są to m.in. koszty energii elektrycznej potrzebnej do podgrzewania cieczy oraz koszty konserwacji i ewentualnych napraw. Regularne czyszczenie i wymiana zużytych części są kluczowe dla utrzymania efektywności działania destylarki oraz jakości uzyskiwanych produktów. Dodatkowo warto pamiętać o kosztach związanych z zakupem surowców wykorzystywanych w procesie destylacji; ceny rozpuszczalników mogą się różnić w zależności od ich rodzaju i jakości.
Jakie nowinki technologiczne wpływają na rozwój destylarek do rozpuszczalnika
Nowinki technologiczne mają ogromny wpływ na rozwój destylarek do rozpuszczalnika, przyczyniając się do zwiększenia ich efektywności oraz bezpieczeństwa użytkowania. W ostatnich latach zauważalny jest trend w kierunku automatyzacji procesów związanych z destylacją; nowoczesne urządzenia często wyposażone są w inteligentne systemy sterujące, które umożliwiają precyzyjne monitorowanie parametrów pracy takich jak temperatura czy ciśnienie. Dzięki tym rozwiązaniom możliwe jest osiągnięcie większej stabilności procesu oraz redukcja ryzyka wystąpienia błędów ludzkich podczas obsługi urządzenia. Kolejnym istotnym aspektem jest rozwój materiałów wykorzystywanych w budowie destylarek; nowe kompozyty czy powłoki ceramiczne zwiększają odporność na korozję i wysokie temperatury, co przekłada się na dłuższą żywotność sprzętu. Innowacyjne technologie chłodzenia również przyczyniają się do poprawy wydajności procesów destylacyjnych; nowoczesne systemy chłodzenia pozwalają na szybsze skraplanie pary oraz lepsze zarządzanie energią wykorzystywaną podczas pracy urządzenia.