Destylator przemysłowy to urządzenie wykorzystywane w procesach separacji cieczy na podstawie różnic w temperaturze wrzenia składników. Jego głównym celem jest uzyskanie czystych substancji chemicznych poprzez oddzielenie ich od zanieczyszczeń lub innych składników. W przemyśle chemicznym, petrochemicznym oraz spożywczym destylatory odgrywają kluczową rolę w produkcji różnych produktów, takich jak alkohole, oleje eteryczne czy paliwa. Proces destylacji polega na podgrzewaniu cieczy do momentu, gdy zaczyna parować, a następnie schładzaniu pary, co prowadzi do jej kondensacji. W ten sposób można oddzielić substancje o różnych temperaturach wrzenia. Destylatory przemysłowe są zazwyczaj bardziej skomplikowane niż te używane w domowych warunkach, ponieważ muszą obsługiwać dużą ilość materiału i zapewniać wysoką efektywność separacji.
Jakie są rodzaje destylatorów przemysłowych i ich zastosowania
W przemyśle istnieje wiele rodzajów destylatorów, które różnią się konstrukcją oraz przeznaczeniem. Najpopularniejsze z nich to destylatory prostokątne, kolumnowe oraz frakcyjne. Destylatory prostokątne są najprostsze w budowie i często stosowane w małych zakładach produkcyjnych. Ich główną zaletą jest łatwość obsługi oraz niskie koszty eksploatacji. Z kolei destylatory kolumnowe charakteryzują się wyższą wydajnością i są stosowane w większych zakładach przemysłowych, gdzie konieczne jest przetwarzanie dużych ilości surowców. Destylacja frakcyjna to proces, który pozwala na oddzielanie wielu składników z jednego surowca jednocześnie, co jest szczególnie przydatne w przemyśle petrochemicznym. W zależności od potrzeb produkcyjnych, wybór odpowiedniego typu destylatora ma kluczowe znaczenie dla efektywności procesu oraz jakości końcowego produktu.
Jakie są kluczowe elementy konstrukcyjne destylatora przemysłowego
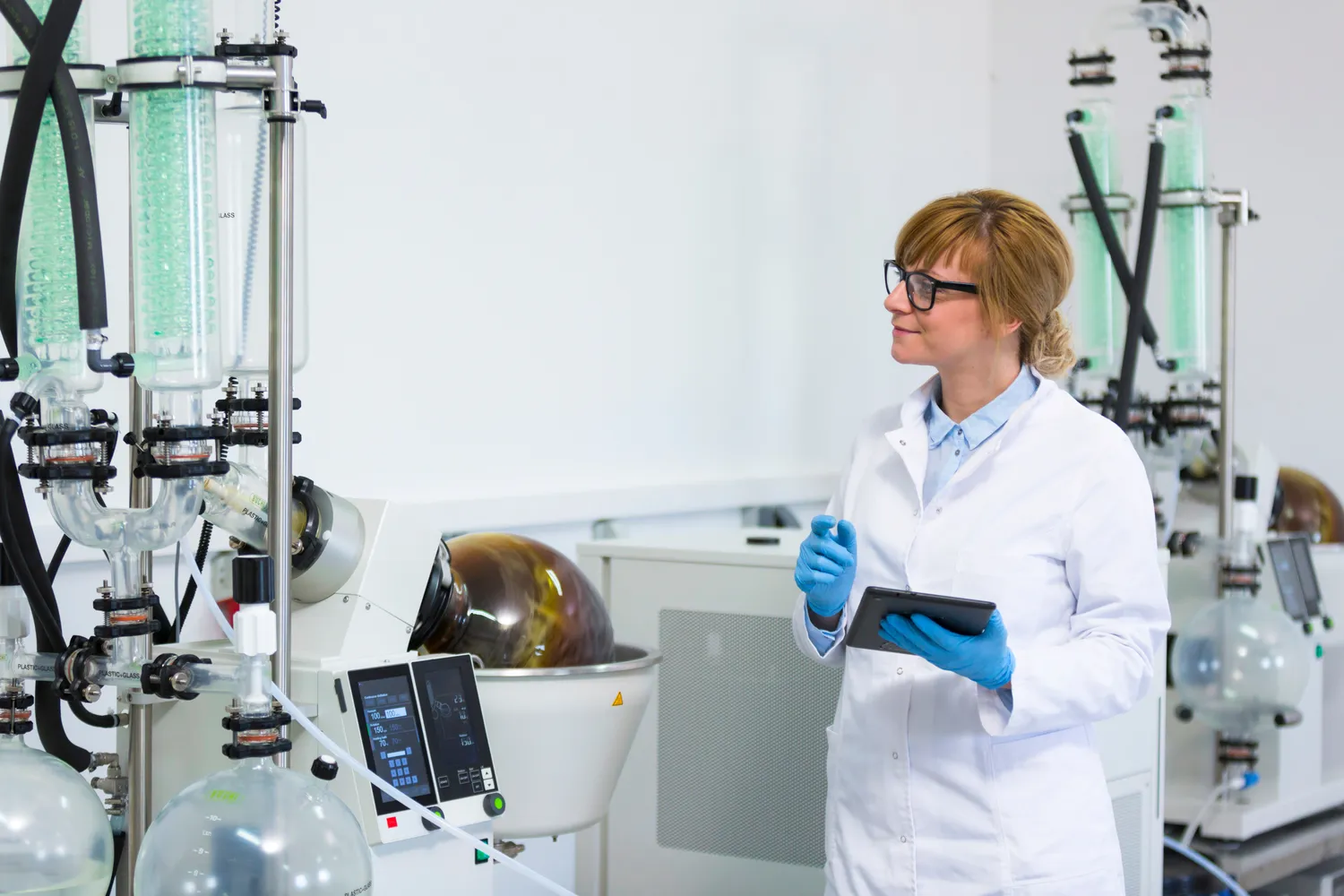
Konstrukcja destylatora przemysłowego składa się z kilku kluczowych elementów, które mają istotny wpływ na jego działanie oraz efektywność procesu destylacji. Podstawowymi komponentami są zbiornik do podgrzewania cieczy, kolumna destylacyjna oraz skraplacz. Zbiornik pełni funkcję miejsca, w którym następuje podgrzewanie surowca do momentu jego wrzenia. Kolumna destylacyjna jest miejscem, gdzie zachodzi właściwy proces separacji składników na podstawie różnic w temperaturze wrzenia. Wewnątrz kolumny znajdują się różnego rodzaju elementy takie jak talerze czy wypełnienia, które zwiększają powierzchnię kontaktu między parą a cieczą, co poprawia efektywność procesu. Skraplacz natomiast odpowiada za kondensację pary powracającej do stanu ciekłego po opuszczeniu kolumny. Dodatkowo istotnymi elementami są systemy kontrolne oraz pompy, które umożliwiają monitorowanie i regulowanie parametrów pracy urządzenia.
Jakie są korzyści z używania destylatorów przemysłowych w produkcji
Używanie destylatorów przemysłowych przynosi wiele korzyści zarówno dla producentów, jak i dla końcowych użytkowników produktów. Przede wszystkim pozwalają one na uzyskanie wysokiej czystości substancji chemicznych poprzez skuteczne oddzielanie zanieczyszczeń oraz innych składników o różnych temperaturach wrzenia. Dzięki temu możliwe jest produkowanie wysokiej jakości alkoholi, olejów eterycznych czy paliw bez niepożądanych dodatków. Kolejną istotną korzyścią jest możliwość przetwarzania dużych ilości surowców w krótkim czasie, co zwiększa efektywność produkcji i obniża koszty operacyjne. Nowoczesne destylatory wyposażone są w zaawansowane systemy automatyzacji i monitorowania procesów, co pozwala na precyzyjne zarządzanie parametrami pracy urządzenia oraz minimalizację ryzyka błędów ludzkich. Dodatkowo stosowanie technologii destylacji przyczynia się do ochrony środowiska poprzez zmniejszenie ilości odpadów oraz emisji szkodliwych substancji do atmosfery.
Jakie są najnowsze technologie w destylacji przemysłowej
W ostatnich latach rozwój technologii w dziedzinie destylacji przemysłowej znacząco wpłynął na efektywność i jakość procesów produkcyjnych. Nowoczesne destylatory są coraz częściej wyposażane w zaawansowane systemy automatyzacji, które umożliwiają monitorowanie parametrów pracy w czasie rzeczywistym. Dzięki temu operatorzy mogą szybko reagować na zmiany warunków, co zwiększa bezpieczeństwo i wydajność procesu. Wprowadzenie technologii takich jak destylacja membranowa czy destylacja z wykorzystaniem ultradźwięków pozwala na jeszcze skuteczniejsze oddzielanie składników, a także zmniejsza zużycie energii. Innowacyjne podejścia, takie jak zastosowanie nanotechnologii w budowie elementów destylacyjnych, przyczyniają się do poprawy efektywności separacji oraz obniżenia kosztów eksploatacji. Dodatkowo, coraz większą rolę odgrywa zrównoważony rozwój i ochrona środowiska, co skłania producentów do inwestowania w technologie minimalizujące negatywny wpływ na otoczenie.
Jakie są wyzwania związane z eksploatacją destylatorów przemysłowych
Eksploatacja destylatorów przemysłowych wiąże się z różnymi wyzwaniami, które mogą wpływać na efektywność procesów oraz jakość uzyskiwanych produktów. Jednym z głównych problemów jest konieczność regularnej konserwacji i czyszczenia urządzeń, aby zapobiec gromadzeniu się osadów oraz zanieczyszczeń, które mogą obniżać wydajność destylacji. Ponadto, zmiany w jakości surowców mogą prowadzić do konieczności dostosowywania parametrów pracy destylatora, co wymaga odpowiedniego przeszkolenia personelu oraz elastyczności w zarządzaniu procesem produkcyjnym. Innym istotnym wyzwaniem są koszty energii, które mogą stanowić znaczną część wydatków operacyjnych zakładów przemysłowych. W związku z tym wiele firm poszukuje sposobów na optymalizację zużycia energii oraz wdrażanie rozwiązań proekologicznych. Dodatkowo, regulacje prawne dotyczące ochrony środowiska oraz bezpieczeństwa pracy stają się coraz bardziej rygorystyczne, co wymusza na przedsiębiorstwach dostosowywanie swoich procesów do nowych norm.
Jakie są najlepsze praktyki w obsłudze destylatorów przemysłowych
Aby zapewnić optymalną wydajność i jakość produktów uzyskiwanych za pomocą destylatorów przemysłowych, warto stosować najlepsze praktyki w ich obsłudze. Przede wszystkim kluczowe jest regularne szkolenie personelu odpowiedzialnego za obsługę urządzeń. Wiedza na temat działania destylatora oraz umiejętność szybkiego reagowania na ewentualne problemy mogą znacząco wpłynąć na efektywność procesu. Ważne jest również prowadzenie szczegółowej dokumentacji dotyczącej parametrów pracy urządzenia oraz jakości surowców, co pozwala na bieżąco monitorować wszelkie zmiany i dostosowywać proces do aktualnych potrzeb. Regularna konserwacja i czyszczenie elementów destylacyjnych to kolejne istotne aspekty, które pomagają utrzymać wysoką wydajność i jakość uzyskiwanych produktów. Należy także zwracać uwagę na dobór odpowiednich surowców oraz ich przygotowanie przed procesem destylacji, aby uniknąć problemów związanych z zanieczyszczeniami czy niepożądanymi reakcjami chemicznymi.
Jakie są zastosowania destylatorów przemysłowych w różnych branżach
Destylatory przemysłowe znajdują szerokie zastosowanie w różnych branżach, co świadczy o ich uniwersalności i znaczeniu w nowoczesnej produkcji. W przemyśle chemicznym służą do produkcji substancji chemicznych o wysokiej czystości, takich jak alkohole czy kwasy organiczne. W branży petrochemicznej wykorzystywane są do separacji frakcji ropy naftowej, co pozwala na uzyskanie paliw oraz innych produktów chemicznych. W przemyśle spożywczym destylatory odgrywają kluczową rolę w produkcji napojów alkoholowych, takich jak whisky czy wódka, gdzie ważne jest uzyskanie odpowiedniej jakości trunku poprzez skuteczną separację składników. Dodatkowo stosowane są do ekstrakcji olejków eterycznych z roślin, co ma zastosowanie w kosmetykach oraz aromaterapii. W ostatnich latach rośnie zainteresowanie wykorzystaniem destylatorów w przemyśle farmaceutycznym do produkcji substancji czynnych leków oraz ich oczyszczania.
Jakie są przyszłe kierunki rozwoju technologii destylacyjnych
Przyszłość technologii destylacyjnych zapowiada się obiecująco dzięki ciągłemu postępowi naukowemu oraz technologicznemu. Jednym z głównych kierunków rozwoju jest dalsza automatyzacja procesów związanych z obsługą destylatorów. Systemy sztucznej inteligencji i uczenia maszynowego będą coraz częściej wykorzystywane do analizy danych operacyjnych oraz optymalizacji parametrów pracy urządzeń. Dzięki temu możliwe będzie osiąganie jeszcze wyższej efektywności procesów oraz redukcja kosztów operacyjnych. Kolejnym istotnym trendem jest rozwój technologii proekologicznych, które mają na celu minimalizację negatywnego wpływu na środowisko naturalne. Wprowadzenie rozwiązań opartych na energii odnawialnej czy recyklingu ciepła może przyczynić się do znacznego obniżenia emisji gazów cieplarnianych oraz zużycia zasobów naturalnych. Również innowacyjne materiały stosowane w budowie elementów destylacyjnych mogą wpłynąć na poprawę efektywności separacji oraz trwałości urządzeń.
Jakie są ekonomiczne aspekty inwestycji w destylatory przemysłowe
Inwestycja w nowoczesne destylatory przemysłowe wiąże się z wieloma aspektami ekonomicznymi, które należy dokładnie przeanalizować przed podjęciem decyzji o zakupie lub modernizacji istniejących urządzeń. Koszt zakupu nowego sprzętu może być znaczny, jednak warto zwrócić uwagę na potencjalne oszczędności wynikające z wyższej efektywności energetycznej oraz jakości uzyskiwanych produktów. Nowoczesne technologie często pozwalają na redukcję kosztów operacyjnych poprzez zmniejszenie zużycia energii czy surowców, a także ograniczenie strat materiałowych podczas procesu produkcyjnego. Dodatkowo warto rozważyć korzyści związane z poprawą jakości produktów końcowych, co może przyczynić się do zwiększenia konkurencyjności firmy na rynku oraz wzrostu jej przychodów ze sprzedaży. Należy również pamiętać o aspektach związanych z regulacjami prawnymi dotyczącymi ochrony środowiska i bezpieczeństwa pracy; inwestycje w nowoczesne technologie mogą pomóc firmom spełnić te wymagania bez konieczności ponoszenia dodatkowych kosztów związanych z karami czy dostosowaniami infrastruktury.