Smarowanie narzędzi pneumatycznych jest kluczowym elementem ich konserwacji oraz zapewnienia długotrwałej wydajności. Warto zacząć od zrozumienia, jakie rodzaje smarów są najodpowiedniejsze do stosowania w narzędziach pneumatycznych. Wiele osób nie zdaje sobie sprawy, że nie każdy smar nadaje się do tych urządzeń. Najlepszym wyborem są smary na bazie silikonu lub smary specjalnie przeznaczone do zastosowań pneumatycznych. Ważne jest również, aby regularnie kontrolować stan narzędzi i ich komponentów, ponieważ nagromadzenie zanieczyszczeń może prowadzić do uszkodzeń. Proces smarowania powinien być przeprowadzany zgodnie z zaleceniami producenta, które można znaleźć w dokumentacji technicznej narzędzia. Warto także pamiętać o tym, aby nie przesadzać z ilością smaru, ponieważ nadmiar może prowadzić do gromadzenia się brudu i pyłu, co w dłuższej perspektywie negatywnie wpłynie na działanie narzędzia.
Jakie są najlepsze metody smarowania narzędzi pneumatycznych
Wybór odpowiedniej metody smarowania narzędzi pneumatycznych ma ogromne znaczenie dla ich efektywności i trwałości. Jedną z najpopularniejszych metod jest stosowanie oleju pneumatycznego, który można wprowadzać bezpośrednio do układu powietrznego. Taki olej działa jako środek smarny oraz zabezpiecza przed korozją wewnętrzne elementy narzędzi. Inną metodą jest ręczne smarowanie poszczególnych części narzędzia, co wymaga większej precyzji i staranności. W przypadku bardziej skomplikowanych narzędzi warto rozważyć użycie automatycznych systemów smarowania, które zapewniają równomierne rozprowadzenie środka smarnego. Niezależnie od wybranej metody, kluczowe jest regularne monitorowanie stanu smaru oraz jego wymiana w odpowiednich odstępach czasu. Warto także zwrócić uwagę na warunki pracy narzędzi – w środowiskach o dużej wilgotności lub zapyleniu konieczne może być częstsze smarowanie, aby zapobiec uszkodzeniom spowodowanym przez zanieczyszczenia.
Jakie są najczęstsze błędy przy smarowaniu narzędzi pneumatycznych
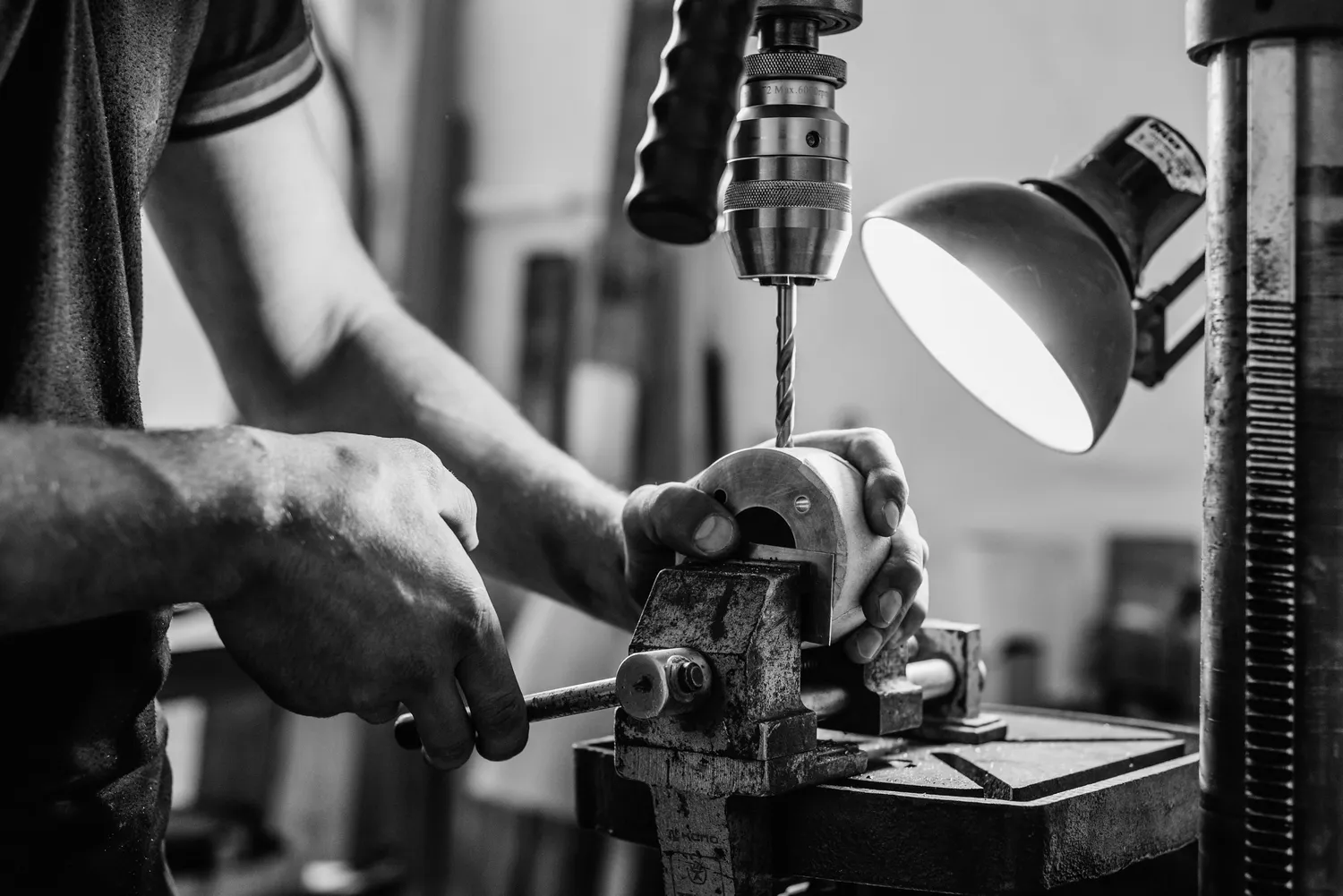
Podczas smarowania narzędzi pneumatycznych wiele osób popełnia typowe błędy, które mogą prowadzić do poważnych problemów w ich działaniu. Jednym z najczęstszych błędów jest używanie niewłaściwego rodzaju smaru, co może skutkować uszkodzeniem elementów wewnętrznych lub zmniejszeniem efektywności działania narzędzia. Kolejnym powszechnym problemem jest nadmierna ilość smaru – wielu użytkowników uważa, że im więcej smaru, tym lepiej, co jest mylnym przekonaniem. Zbyt duża ilość środka smarnego może prowadzić do gromadzenia się brudu oraz pyłu, co negatywnie wpływa na pracę narzędzia. Inny błąd to brak regularnej konserwacji i czyszczenia narzędzi, co prowadzi do nagromadzenia zanieczyszczeń i skrócenia żywotności urządzeń. Ważne jest również ignorowanie zaleceń producenta dotyczących częstotliwości i sposobu smarowania – każda maszyna ma swoje specyficzne wymagania, których należy przestrzegać.
Jak często należy smarować narzędzia pneumatyczne
Częstotliwość smarowania narzędzi pneumatycznych zależy od wielu czynników, takich jak intensywność użytkowania czy warunki pracy. W przypadku profesjonalnych zastosowań zaleca się regularne sprawdzanie stanu smaru co kilka dni lub nawet codziennie w przypadku intensywnej eksploatacji. Dla mniej intensywnych zastosowań wystarczy kontrolować stan smaru co kilka tygodni lub miesięcy. Ważne jest również dostosowanie częstotliwości do specyfiki danego narzędzia – niektóre modele mogą wymagać częstszego serwisowania niż inne ze względu na swoją konstrukcję lub przeznaczenie. Należy również pamiętać o tym, że warunki pracy mają ogromny wpływ na potrzebę smarowania; w środowiskach o dużym zapyleniu lub wilgotności konieczne może być częstsze serwisowanie niż w warunkach suchych i czystych. Regularne monitorowanie stanu narzędzi oraz ich komponentów pozwala na szybką reakcję w przypadku zauważenia jakichkolwiek nieprawidłowości czy oznak zużycia.
Jakie są zalety regularnego smarowania narzędzi pneumatycznych
Regularne smarowanie narzędzi pneumatycznych przynosi szereg korzyści, które mają kluczowe znaczenie dla ich wydajności oraz trwałości. Przede wszystkim, odpowiednie smarowanie zmniejsza tarcie pomiędzy ruchomymi częściami narzędzia, co przekłada się na mniejsze zużycie elementów mechanicznych. Dzięki temu narzędzia działają płynniej i bardziej efektywnie, co z kolei wpływa na jakość wykonywanych prac. Ponadto, regularne smarowanie chroni przed korozją, co jest szczególnie istotne w przypadku narzędzi eksploatowanych w trudnych warunkach atmosferycznych. Utrzymanie odpowiedniego poziomu smaru pozwala także na lepsze odprowadzanie ciepła, co minimalizuje ryzyko przegrzewania się narzędzi podczas intensywnej pracy. Warto również zauważyć, że dobrze utrzymane narzędzia pneumatyczne są mniej podatne na awarie, co prowadzi do zmniejszenia kosztów napraw oraz przestojów w pracy. Regularne smarowanie to także kluczowy element dbania o bezpieczeństwo użytkowników – sprawne narzędzia są mniej skłonne do niespodziewanych awarii, które mogą prowadzić do kontuzji.
Jakie akcesoria ułatwiają smarowanie narzędzi pneumatycznych
Aby skutecznie smarować narzędzia pneumatyczne, warto zaopatrzyć się w odpowiednie akcesoria, które znacznie ułatwią ten proces. Jednym z najważniejszych elementów jest olejarka pneumatyczna, która umożliwia precyzyjne dozowanie oleju do układu powietrznego. Dzięki temu można uniknąć nadmiaru smaru oraz zapewnić równomierne rozprowadzenie środka smarnego wewnątrz narzędzia. Innym przydatnym akcesorium jest zestaw do czyszczenia narzędzi pneumatycznych, który pozwala na usunięcie zanieczyszczeń i resztek smaru przed nałożeniem nowego środka smarnego. Warto również zainwestować w specjalistyczne środki czyszczące przeznaczone do konserwacji sprzętu pneumatycznego. Dodatkowo, użycie pistoletu do smarowania może znacznie przyspieszyć proces aplikacji oleju, zwłaszcza w przypadku większych narzędzi lub maszyn przemysłowych. Nie można zapominać o rękawicach ochronnych i okularach zabezpieczających, które powinny być noszone podczas pracy z chemikaliami i środkami smarnymi.
Jakie są objawy niewłaściwego smarowania narzędzi pneumatycznych
Niewłaściwe smarowanie narzędzi pneumatycznych może prowadzić do szeregu problemów, które mogą być łatwo zauważalne przez użytkowników. Jednym z pierwszych objawów jest zwiększone tarcie podczas pracy narzędzia, co może objawiać się hałasem lub drganiami. Takie symptomy wskazują na to, że ruchome części nie są odpowiednio nasmarowane i mogą szybko ulegać zużyciu. Kolejnym sygnałem alarmowym jest spadek wydajności narzędzia – jeśli urządzenie nie działa tak efektywnie jak wcześniej, może to być oznaką braku odpowiedniego smaru lub jego degradacji. W przypadku zauważenia wycieków oleju lub innego środka smarnego należy natychmiast podjąć działania naprawcze, ponieważ może to prowadzić do poważnych uszkodzeń mechanicznych. Inne objawy to trudności w uruchamianiu narzędzia czy też jego nagłe zatrzymanie podczas pracy. Zbyt mała ilość smaru może również prowadzić do przegrzewania się urządzenia, co z kolei zwiększa ryzyko awarii silnika lub innych kluczowych komponentów.
Jakie środki ostrożności zachować przy smarowaniu narzędzi pneumatycznych
Podczas smarowania narzędzi pneumatycznych niezwykle istotne jest przestrzeganie zasad bezpieczeństwa oraz stosowanie odpowiednich środków ostrożności. Przede wszystkim należy zawsze zapoznawać się z instrukcjami producenta dotyczącymi stosowania środków smarnych oraz konserwacji danego urządzenia. Używanie niewłaściwych substancji chemicznych może prowadzić do uszkodzenia sprzętu lub nawet stanowić zagrożenie dla zdrowia użytkownika. Ważne jest także noszenie odpowiednich środków ochrony osobistej, takich jak rękawice czy okulary ochronne, aby zminimalizować ryzyko kontaktu ze szkodliwymi substancjami chemicznymi. Należy również pracować w dobrze wentylowanym pomieszczeniu lub na świeżym powietrzu, aby uniknąć wdychania oparów oleju czy innych środków smarnych. Podczas aplikacji środka smarnego warto unikać kontaktu z gorącymi powierzchniami oraz ruchomymi częściami urządzenia – najlepiej poczekać aż sprzęt ostygnie po intensywnej pracy.
Jakie są różnice między różnymi rodzajami olejów do narzędzi pneumatycznych
Wybór odpowiedniego oleju do narzędzi pneumatycznych ma kluczowe znaczenie dla ich prawidłowego funkcjonowania i długowieczności. Na rynku dostępnych jest wiele różnych rodzajów olejów, które różnią się składem chemicznym oraz właściwościami fizycznymi. Oleje mineralne są najczęściej stosowane ze względu na swoją dostępność i niską cenę; jednakże mogą one nie zapewniać wystarczającej ochrony przed korozją i utlenianiem w trudnych warunkach pracy. Z kolei oleje syntetyczne oferują lepszą stabilność termiczną oraz odporność na utlenianie, co czyni je idealnym wyborem dla intensywnie eksploatowanych narzędzi pneumatycznych. Oleje silikonowe charakteryzują się doskonałą odpornością na wysokie temperatury oraz działanie chemikaliów; są szczególnie polecane do zastosowań wymagających dużej precyzji i niezawodności działania. Warto również zwrócić uwagę na oleje biodegradowalne, które stają się coraz bardziej popularne ze względu na rosnącą świadomość ekologiczną; takie produkty oferują dobre właściwości smarne przy jednoczesnym minimalizowaniu negatywnego wpływu na środowisko naturalne.
Jakie są najlepsze praktyki konserwacji narzędzi pneumatycznych
Aby zapewnić długotrwałe i efektywne działanie narzędzi pneumatycznych, warto wdrożyć najlepsze praktyki konserwacji tych urządzeń. Regularna kontrola stanu technicznego powinna być priorytetem – zaleca się przeglądanie wszystkich elementów roboczych pod kątem zużycia czy uszkodzeń co najmniej raz w miesiącu. Oprócz tego należy systematycznie czyścić filtry powietrza oraz wymieniać je zgodnie z zaleceniami producenta; czyste filtry zapewniają optymalny przepływ powietrza i chronią przed zanieczyszczeniami wewnętrznymi urządzenia. Warto również pamiętać o regularnym sprawdzaniu poziomu oleju i jego jakości; jeśli zauważymy jakiekolwiek nieprawidłowości, należy natychmiast podjąć działania naprawcze lub wymienić olej na nowy. Dobrą praktyką jest także przechowywanie narzędzi w suchym i czystym miejscu – wilgoć oraz kurz mogą negatywnie wpłynąć na ich stan techniczny i wydajność pracy.